Using Fuji Prescale To Check Surface Defects of Paper Size Rubber Rollers
Keywords: : rubber roller surface defect, paper wrinkling defect, wedging of rubber rollersSummary: Rubber rollers are used to manufacture various sizes and thickness of paper. Defective rubber surface causes poor quality of paper, and Fuji Prescale Film is the only fast, reliable and cheap diagnostics tool to visualize any surface defects of paper size rubber rollers.
Written by Igor Mateski
Paper Size Rubber Rollers Usage
The paper manufacturing industry heavily relies on rubber rollers to manufacture various sizes and paper thickness to match the clients' needs. To achieve these size and thickness variances, manufacturers replace sizing rubber rollers.
Depending on the manufacturing process, the rollers exchange can be a lengthy and expensive procedure as in some processes there are more sets of rollers that impede access to the sizing rollers, as shown on the images below:
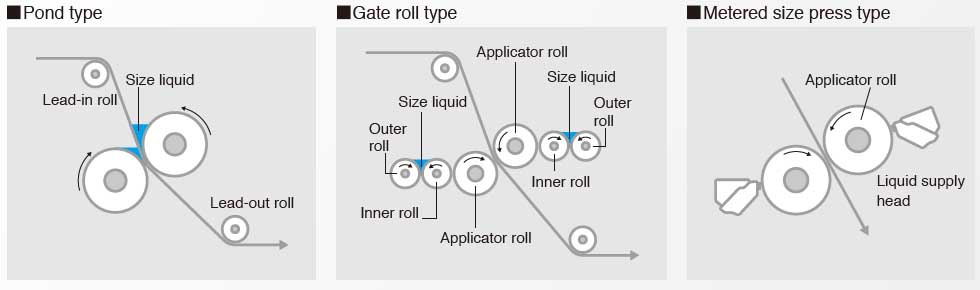
Depending on the type of rolling machine, exchanging size rollers can be as simple as replacing the two rollers (in Pond-type machines) or complete disassembly of the machine (gate roll and metered presses).
Defects of Rubber Rollers
Size rubber rollers suffer from surface defects just as any other rubber roller:
- scratches/dents of the surface
- poor adhesion of the rubber sleeve with the iron core
- friction tare resulting to poor peripheral tactile pressure
This results in uneven paper thickness, where the peripheral several inches are thicker than the nominal thickness that is found in the mid section of the rollers. Moreover, diameter reduction at the peripheral zones nullifies the needed larger peripheral speed difference that causes paper to wrinkle:
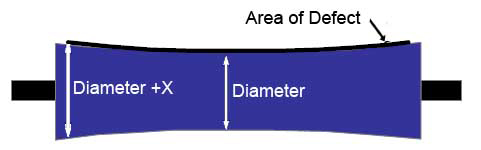
The image above is an illustration of how diameter differences are manufactured into the rubber sleeve to achieve proper surface speed and prevent wrinkling. Ware and tare reduce the diameter difference and peripheral speed evens out along the entire roller surface, which in turn causes wrinkling and paper thickness inconsistencies
Fast Surface Checking With Fuji Prescale
Service technicians will have to spent a lot of time and material to establish if the size rubber rollers are damaged as the only diagnostic procedure is to look at the manufactured paper rolls. This is both time consuming and expensive.
Using the Fuji Prescale film LLW (super-low pressure range film) can significantly reduce the diagnostics time and expenses by directly measuring the tactile pressure along the entire rubber roller surface, as shown on the illustration below:
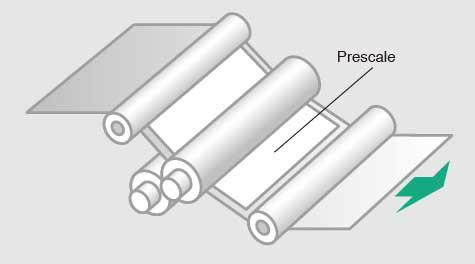
Thanks to the Fuji Prescale LLW direct pressure measurement, technicians do not need long paper batches to verify if there is any surface defects of the size rollers. Also, subjective elements like guess-work, intuition and experience are unneeded. Technicians can easily place a Fuji Prescale film inside the machine and directly read out the tactile pressure from the developed Fuji Prescale film, as shown on the image below:
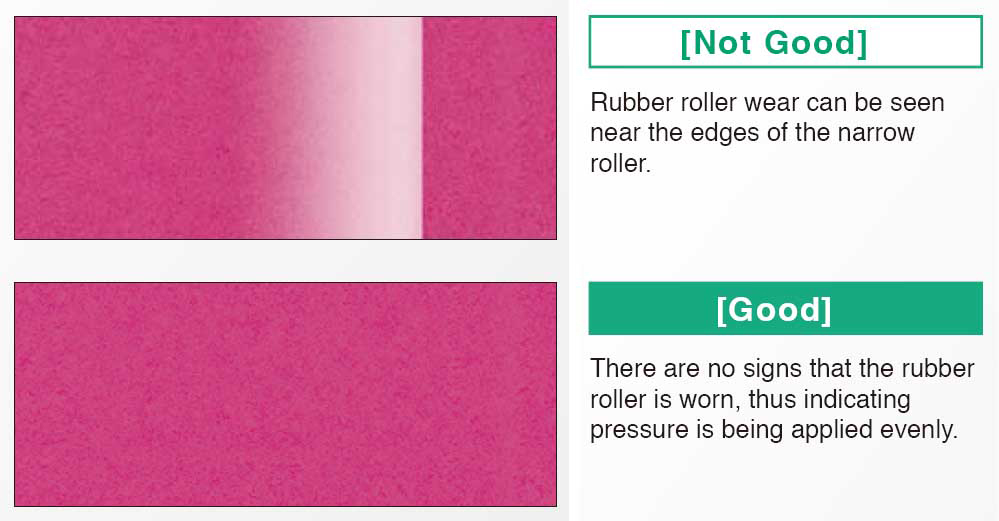
The first image of a developed Fuji Prescale film shows a clear edge in the rubber surface that is caused by long period of usage. This wedge may be enough to cause paper wrinkling and will definitely cause inconsistent paper thickness. Thanks to this direct tactile pressure measurement, technicians can easily determine the state of the rubber surface and establish if a roller replacement is due. With such a fail-sage, fast and cheap test, technicians have no need of long years of experience or veteran intuition to determine that this roller set needs replacement.
After replacement, another test is required to verify that the new rollers are positioned properly and that there is no pressure hotspots along the rubber surface. The image below shows a developed Fuji Prescale film of a roller set that has no surface defects.
Thanks to the Fuji Prescale LLW pressure sensitive film, repair technicians can quickly establish a correct diagnosis and intervene only when needed. With this direct pressure readout procedure, there is no need of guesswork, no need of material waste, and most importantly, such tests can be done regularly so that manufacturers can ensure constant quality production.